DCS主要用于工艺自动化,PLC(可编程逻辑控制器)主要用于工厂自动化(生产线)。
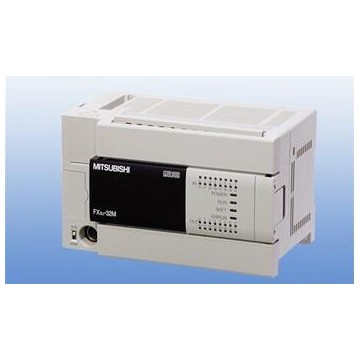
从这个角度来看,如果计算机和网络,它们是统一的,有差异,主要集中在应用程序的需求,DCS通常需要先进的控制算法,如在炼油工业中,PLC处理速度要求高,因为经常使用联锁,甚至故障安全系统、SCADA也有一些特殊要求,如振动监测、流量计算,和山谷负载调整等。
SCADA是调度管理,DCS是工厂管理,PLC是现场设备层。PLC系统,可编程控制器,适用于工业现场测控,现场测控功能强,性能稳定,可靠性高,技术成熟,用途广泛,价格合理。
DCS系统,即分布式控制系统,是20世纪90年代国际先进水平的大型控制系统。适用于测量控制点多、测量控制精度高、测量控制速度快的工业领域。它的特点是分散控制和集中监测。
SCADA系统,即分布式数据采集与监控系统,是一种中小型规模的测控系统。重点介绍了PLC系统强场测量和控制功能的两个优点,以及DCS系统的网络通信能力。
PLC和DCS从早期不同的产品形式和应用发展而来。可以说,PLC是从制造中继发展而来的。DCS是从过程控制仪器发展而来的。每一种产品都有自己的用途和特点,随着技术的发展,行业的渗透和激烈的竞争。PLC和DCS在相互渗透的过程中都在发展各自的优势。需要注意的是,PLC的逻辑控制功能非常强大,但循环控制却不值得一提[看看稍老的PLC模型],而DCS系统恰恰相反。这是由于两种系统的内部处理机制不同造成的。现在怎么样?现有的可编程控制器制造商涉及到西门子和罗克韦尔等DCS应用,它们的系统不过是PLC加上网络加上软件加上增强的控制器。像霍尼韦尔这样的DCS制造商也在他们的系统中加入了PLC,以增强他们的逻辑控制能力。注意,PLC是一种控制器;DCS是一个由控制器+IO集合+网络+软件组成的体系结构。SCADA系统是另一个由系统表示的应用程序需求的概念。顾名思义:分布式数据采集监控系统,它的起源和应用产生的前两个是不同的,主要用于数据收集、监控系统等电力、石油管道监测系统,其特点是分散控制的点,一个系统可能覆盖方圆数千功能(如北美的石油和天然气管道监测系统),通信结构复杂,无法与一般控制系统(从光纤到无线甚至卫星通信)相媲美。其基本单元RTU。
SCADA的重点是监控和控制,可以实现部分逻辑功能,主要用于上位。PLC实现简单的逻辑功能和控制,不提供人机界面。操作需要借助按钮指示灯HMI、SCADA系统进行。DCS具有两种功能,但一般用于大型系统和一些控制要求较高的系统,而且成本较高。这三个人互相渗透。在一些生产企业中,有三个系统。SCADA是生产管理水平的上层控制。DCS实现复杂控制,PLC实现单机控制和简单控制。